Porsche has launched an ambitious pilot project to recycle high-voltage batteries from electric vehicles, aiming to recover valuable raw materials and reuse them in new battery production. This three-phase initiative could help the company reduce its dependence on newly mined resources while addressing growing environmental concerns about EV battery disposal.
From Old Batteries to New: How It Works
The recycling process starts with breaking down used high-voltage batteries from development vehicles. These batteries are mechanically shredded and turned into a dark granulate mixture called “black mass.” This mixture contains critical materials like nickel, cobalt, manganese, and lithium – all essential for making new batteries.
So far, Porsche has produced about 65 tons of this black mass in the first phase of the project. The company is now moving to the second phase, where this material will be further refined and separated into pure raw materials.
“With the help of innovative recycling processes, we strive to increase our independence from volatile and geopolitically unstable raw material markets,” says Barbara Frenkel, Executive Board Member for Procurement at Porsche. “Circular Economy is a core pillar of our sustainability strategy, and with this pilot project, we want to underscore our ambitions.”
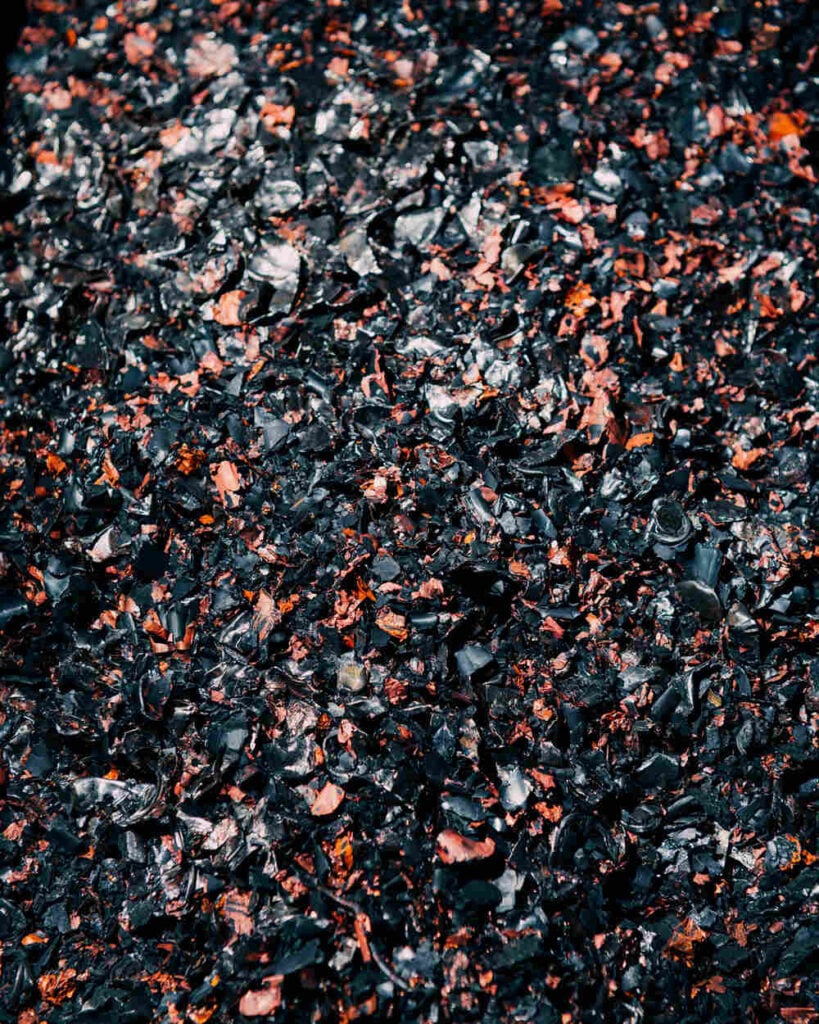
Quality Remains Priority
For taking the full advantage of recycling, the recovered materials’ quality must equal the freshly mined materials’ quality. For the good performance of the super cars, purity and quality matter a lot, and the biggest thing is the Porsche brand name attached with it. So, it must be top-grade material after recycling.
In the third and final phase of the pilot, Porsche plans to produce high-voltage battery cells containing a defined percentage of these recycled materials. These will be tested thoroughly to see if they can match the performance needs of future Porsche electric vehicles.
Similar Posts:
Beyond Environmental Benefits
Removing their dependence on the new mining materials is a strategic and environmental decision; there will be many other benefits as well.
By developing its own recycling capabilities, Porsche aims to:
- Secure its supply chain for critical battery materials
- Reduce vulnerability to price fluctuations in raw material markets
- Prepare for upcoming European Union battery regulations expected to come into effect around 2031
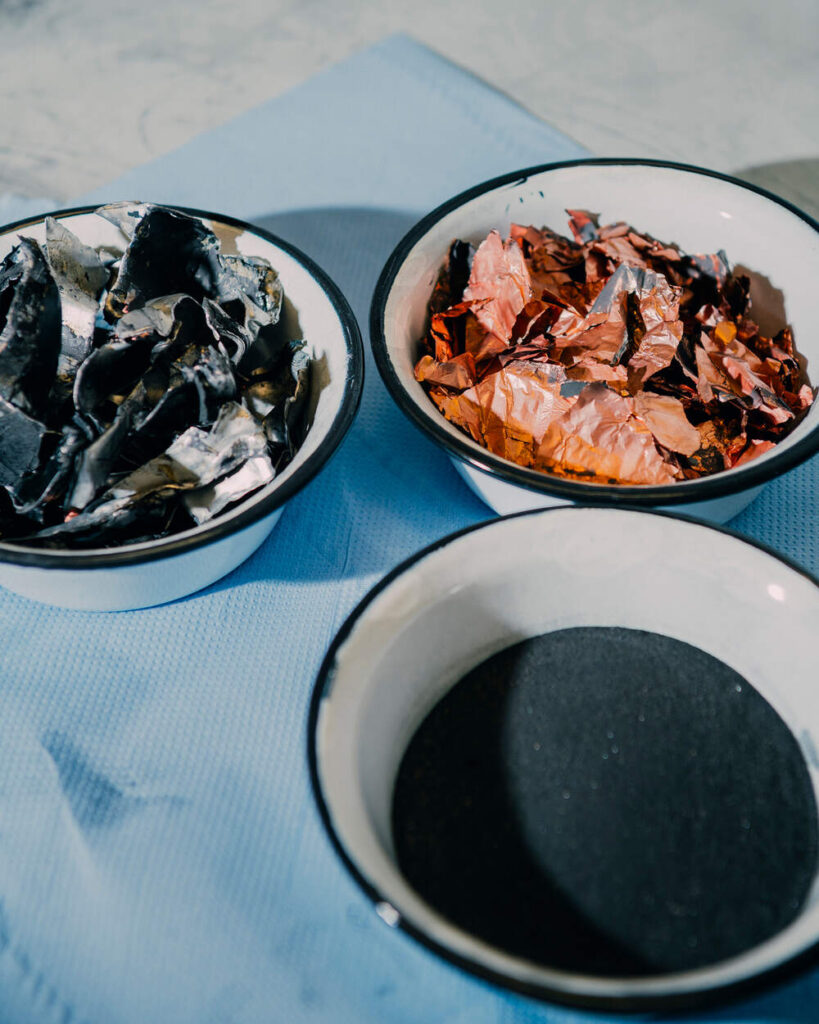
Looking Ahead: Building a Recycling Network
This pilot project is just the start of Porsche’s battery recycling ambitions. The company plans to establish a broader recycling network for high-voltage batteries in collaboration with external partners. This would create a true circular economy where valuable materials from old batteries directly feed into the production of new ones.
The initiative is part of Porsche’s wider commitment to sustainability. Beyond battery recycling, the company is also working on using more environmentally friendly materials and remanufacturing vehicle components to extend their useful life.
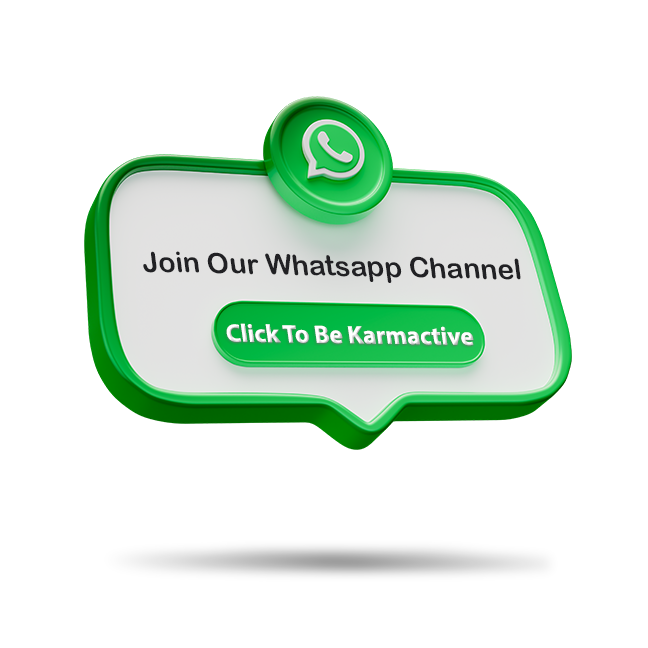
While the technology shows promise, scaling up to handle the growing number of end-of-life EV batteries in the coming years will present new challenges as the electric vehicle market continues to expand.
Nevertheless, as electric vehicle adoption continues to grow worldwide, initiatives like Porsche’s battery recycling program represent an important step toward making EVs more sustainable throughout their entire lifecycle.
Frequently Asked Questions
Porsche has launched a pilot project to recycle high-voltage batteries from electric vehicles. They’re breaking down used batteries to recover valuable materials like nickel, cobalt, manganese, and lithium. These recovered materials will be refined and potentially used to make new batteries for future Porsche electric vehicles, creating a closed-loop system that reduces waste and the need for new mining.
In battery recycling, “black mass” refers to the dark granulate mixture that’s created when old batteries are mechanically shredded. This mixture contains valuable raw materials like nickel, cobalt, manganese, and lithium that can be extracted and refined. Porsche has already produced about 65 tons of this black mass in the first phase of their recycling project. The black mass goes through further refinement processes to separate out the individual metals for reuse.
Porsche emphasizes that quality and purity are critical concerns in their recycling process. For recycled materials to be used in new Porsche vehicles, they must meet the same high standards as newly mined resources. The company is conducting thorough testing to ensure that batteries made with recycled content will deliver the same performance as those made with new materials. The third phase of their pilot project will specifically test battery cells containing recycled materials to verify they meet Porsche’s performance requirements.
Porsche is investing in battery recycling for several strategic reasons beyond environmental benefits. By developing their own recycling capabilities, they aim to secure their supply chain for critical battery materials and reduce vulnerability to price fluctuations in volatile raw material markets. The initiative also helps them prepare for upcoming European Union battery regulations expected around 2031. According to Barbara Frenkel, Executive Board Member for Procurement at Porsche, “Circular Economy is a core pillar of our sustainability strategy.”
Battery recycling helps the environment by reducing the need for new mining activities, which can cause significant land disruption and pollution. By recovering materials from existing batteries, less energy is consumed compared to extracting and processing new raw materials. A closed-loop recycling system also reduces waste from discarded batteries that might otherwise end up in landfills. As electric vehicle adoption grows worldwide, responsible battery recycling becomes increasingly important for ensuring that EVs are truly sustainable throughout their entire lifecycle.
EV battery recycling faces several challenges. The process requires sophisticated technology to achieve high recovery rates and sufficient purity of materials. Scaling up recycling operations to handle the growing number of end-of-life batteries will be difficult as electric vehicle adoption increases. Creating efficient collection systems for used batteries and ensuring the economic viability of recycling operations are also significant hurdles. Additionally, different battery chemistries may require different recycling approaches. Despite these challenges, companies like Porsche are making investments now to develop solutions for the future.