Plasma-polymerized plant extracts are creating microporous hydrophobic barriers on cellulosic substrates at Fraunhofer Institute for Surface Engineering and Thin Films IST, offering a biochemical solution to Germany’s packaging waste challenge. The BioPlas4Paper project employs atmospheric pressure plasma discharge systems operating at 70°C to activate unsaturated fatty acid chains from oregano oil, chia oil, and bark-derived extractives.
“We employ atmospheric pressure plasma technology, where gas is excited with high voltage under ambient pressure to generate plasma, i.e., a particle mixture of ions, free electrons and, in most cases, neutral atoms or molecules. The process causes a discharge between the electrodes,” explains Martin Bellmann of Fraunhofer IST. The plasma-enhanced chemical vapor deposition (PECVD) process transforms these bio-based precursors into crosslinked polymer networks through free radical polymerization mechanisms.
The technical architecture features rotationally symmetric electrodes generating nitrogen-based plasma fields. The geometric configuration prevents ambient air interference – a critical innovation for maintaining coating uniformity at industrial processing speeds. “At high processing speeds, the roughness of the paper’s surface causes turbulence in the ambient air, altering the properties of the plasma. We can avoid these detrimental effects with our concept,” Bellmann notes. The plasma source maintains precise proximity to the cellulosic substrate, achieving complete displacement of ambient air.
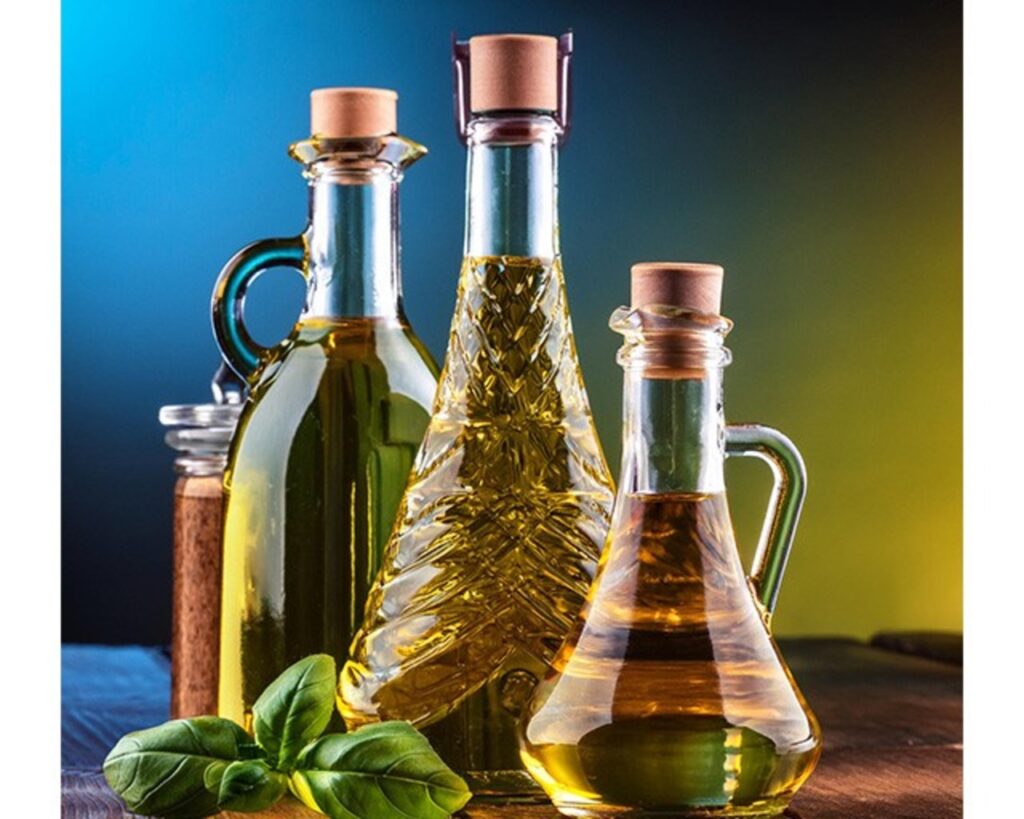
Laboratory analysis confirms successful formation of uniform hydrophobic barriers using olive oil precursors. The resulting plasma polymers penetrate the paper’s microstructure, creating covalent bonds with cellulose fibers. These molecular-level interactions create water-repellent surfaces while maintaining the paper’s natural biodegradability.
The Technical University of Darmstadt contributes expertise in polymer chemistry and surface characterization, while the Thünen Institute of Wood Research provides advanced cellulose analytics. The coatings maintain structural integrity at plasma temperatures of around 70 degrees Celsius, preserving both the paper substrate and bio-based precursor molecules.
Current packaging solutions rely heavily on polyethylene and polypropylene barriers, which persist in soil for 400+ years. The BioPlas4Paper coatings decompose through natural biochemical processes, aligning with EU Directive 2019/904 requirements for reduced plastic packaging.
Paper packaging’s USD 416.5 billion market (2022) races toward USD 503.1 billion by 2028, propelled by consumer demand for circular-economy materials. The shift reflects a growing need for reusable, recyclable cellulose-based substrates as plastic alternatives in the packaging sector.
More Stories
Scale-up parameters focus on optimizing plasma power density (watts/cm² ), precursor flow rates (mL/min ), and web speeds (m/min). Oxygen transmission rate (OTR) measurements show values below 100 cm³/(m²•day), meeting food packaging requirements.
The research team continues investigating bark extractives rich in polyphenolic compounds, which exhibit antibacterial effects. Moving box prototypes demonstrated resistance to extended periods of rain without becoming soft, maintaining structural integrity throughout exposure.
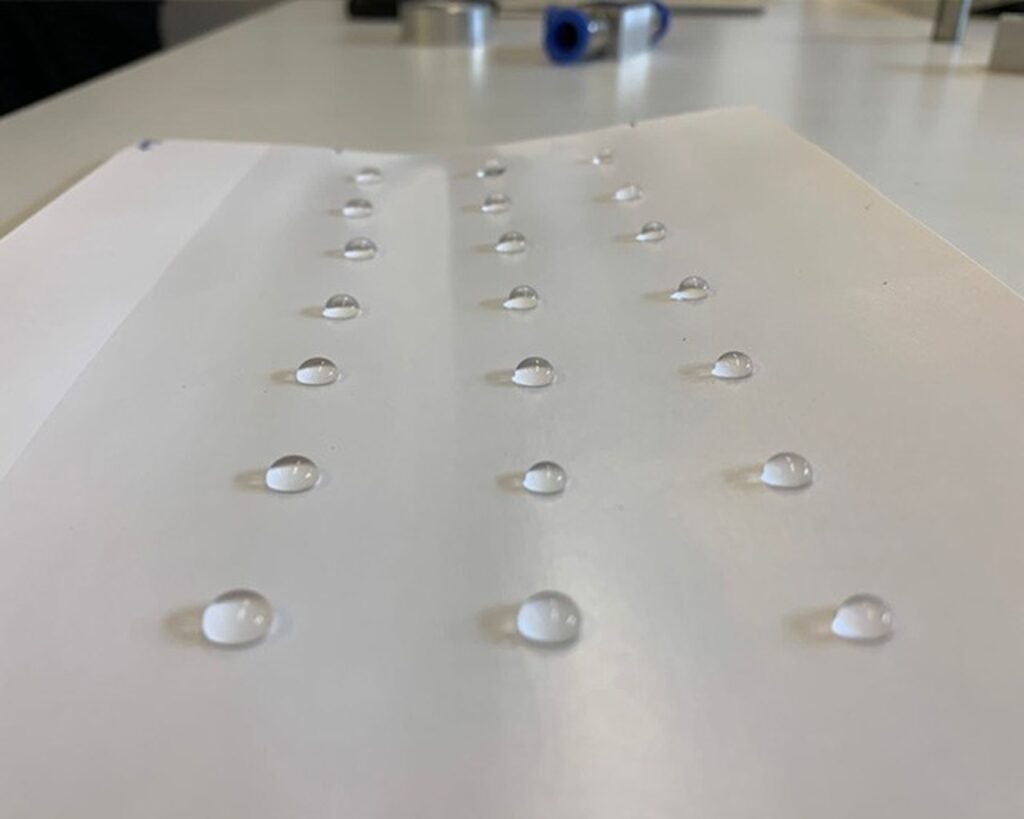
Real-time plasma diagnostics enable monitoring of coating chemistry. The team employs various analytical methods to confirm retention of key functional properties after plasma treatment. Among other properties, these plant substances exhibit antibacterial effects .
Current research focuses on optimizing coating parameters for different paper grades. The project partners aim to prepare paper for increasingly sophisticated use cases and to replace plastic materials in the future. As Bellmann states, “Our objective is to reduce dependence on fossil resources and support the transition to a resource-efficient economy.”
Market implementation requires meeting industry standards and regulations. The research team collaborates with partners to validate coating performance under industrial conditions, ensuring consistent and reproducible results even at higher coating speeds.