Researchers at the University of Missouri have created a novel 3D printing machine that combines multiple materials to produce complex devices. This innovation, dubbed the Freeform Multi-material Assembly Process (FMAP), allows for the creation of multi-layered sensors, circuit boards, and textiles with embedded electronic components using a single machine.
The technology, detailed in a recent Nature Communications paper, utilizes plastics, metals, and semiconductors to fabricate intricate structures. FMAP employs a three-nozzle system: one for adding ink-like material, another for laser carving, and a third for enhancing functional capabilities.
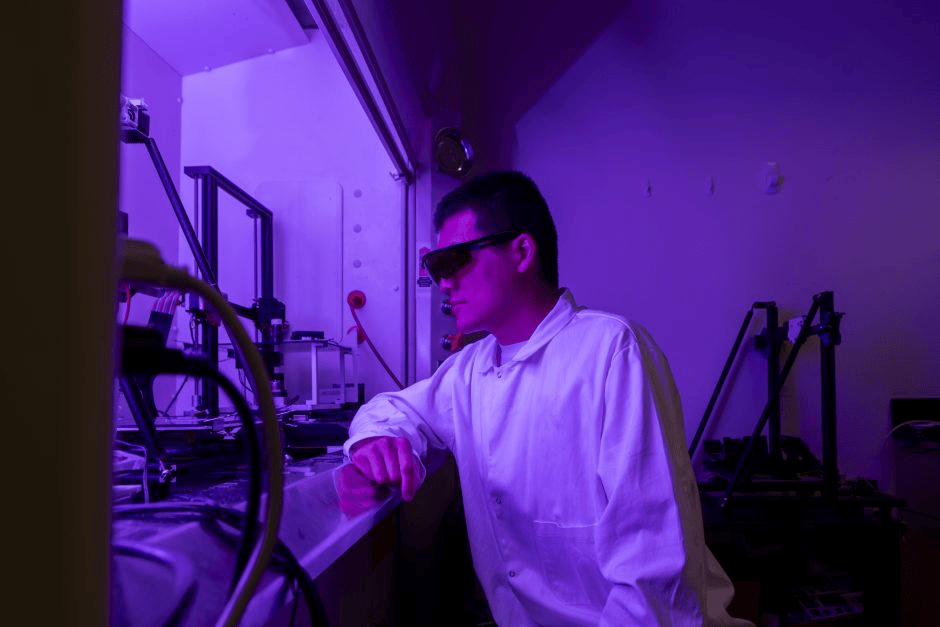
Bujingda Zheng, the study’s lead author and a doctoral student in mechanical engineering, said, “This is the first time this type of process has been used, and it’s unlocking new possibilities. I’m excited about the design. I’ve always wanted to do something that no one has ever done before, and I’m getting to do that here at Mizzou.”
Similar Posts
The process begins with standard 3D printing filament, such as polycarbonate, to create a basic structure. A laser then converts specific parts into laser-induced graphene, followed by the addition of materials to enhance functionality.
This technology offers several advantages over traditional manufacturing methods:
- Efficiency: FMAP streamlines the production of multi-layered structures, reducing time and costs associated with multiple-step processes.
- Versatility: The machine can work with various materials, expanding potential applications.
- Precision: FMAP allows for accurate placement of smaller components within larger 3D structures.
- Sustainability: The process minimizes waste compared to conventional manufacturing techniques.
Potential applications include wearable health monitors, customizable robots, and medical devices. The technology could also benefit environmental research, with the ability to create sensors embedded in natural-looking objects like rocks or seashells for ocean water movement measurements.
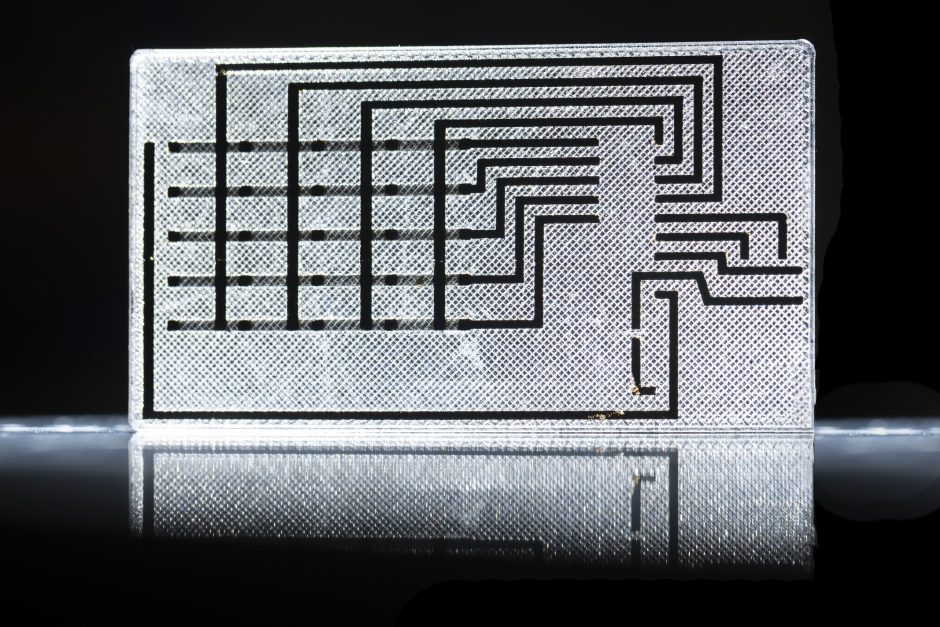
Jian “Javen” Lin, an associate professor of mechanical and aerospace engineering at Mizzou, stated, “This opens the possibility for entirely new markets. It will have broad impacts on wearable sensors, customizable robots, medical devices and more.”
The research is funded by the National Science Foundation (NSF) Advanced Manufacturing program, with additional support from the NSF I-Corps™ program for commercialization exploration.
While FMAP shows promise, it’s worth noting that the 3D printing industry has seen rapid advancements in recent years. Companies and researchers should carefully consider the long-term viability and potential obsolescence of new technologies before making significant investments.
The University of Missouri’s innovation comes at a time when additive manufacturing is gaining traction across industries. According to a report by Grand View Research, the global 3D printing market size was valued at $20.37 billion in 2023 and is expected to expand at a compound annual growth rate (CAGR) of 23.5% from 2024 to 2030.
As 3D printing technology continues to evolve, it will be crucial for businesses and researchers to stay informed about new developments and their potential impact on manufacturing processes and product design.