The automotive industry’s shift toward sustainable manufacturing reached a new milestone as Mercedes-Benz launched Europe’s first battery recycling plant with an integrated mechanical-hydrometallurgical process in Kuppenheim, Germany, on October 21, 2024. The facility operates with a recovery rate exceeding 96% for critical materials like lithium, nickel, and cobalt.
“The circular economy acts as a growth engine and an essential building block for achieving our climate targets,” said Federal Chancellor Olaf Scholz during the opening ceremony. The plant’s development required an investment in the tens of millions of euros, strengthening Germany’s position in sustainable automotive manufacturing.
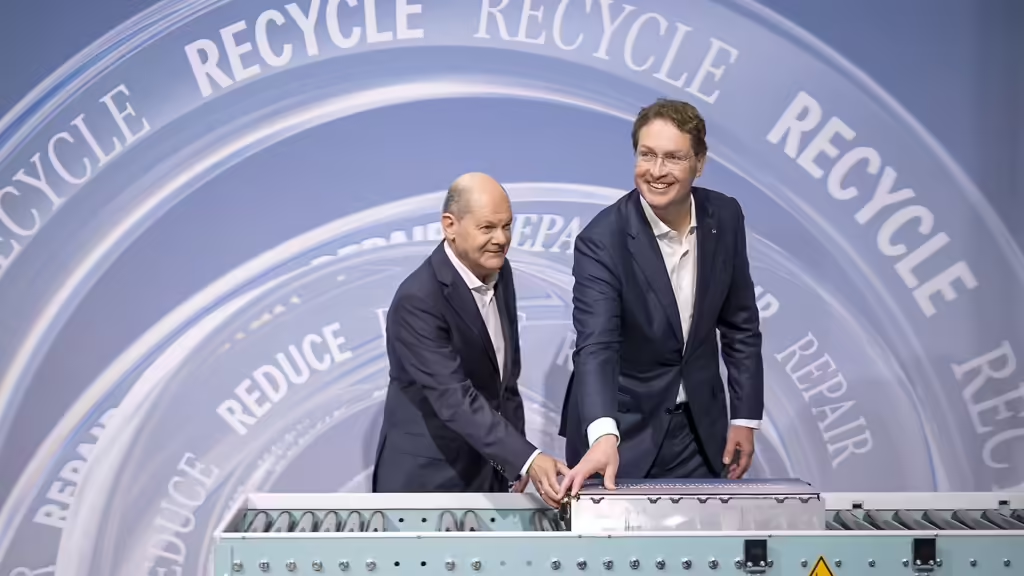
The 6,800-square-meter facility employs an energy-efficient hydrometallurgical process, operating at temperatures up to 80°C – considerably lower than traditional pyrometallurgical methods. This approach reduces both energy consumption and material waste. The plant runs on 100% renewable electricity, supported by a rooftop photovoltaic system generating over 350 kilowatts at peak capacity.
Technical specifications reveal the plant’s annual processing capacity of 2,500 tonnes, sufficient to produce materials for more than 50,000 battery modules for new Mercedes-Benz electric vehicles. The recycling process begins with mechanical separation of plastics, copper, aluminum, and iron, followed by hydrometallurgical treatment of the black mass – the active materials from battery cell electrodes.

“We are systematically deepening our expertise in the battery value chain,” explained Jörg Burzer, Board Member responsible for Production at Mercedes-Benz Group AG. “The innovative technology enables us to recover valuable raw materials from the battery with the highest possible degree of purity.”
Similar Posts:
The project emerged from a partnership between Mercedes-Benz and Primobius, a joint venture of SMS group and Neometals. The German Federal Ministry for Economic Affairs and Climate Action supports the initiative through research collaboration with three German universities, focusing on logistics and reintegration concepts.
Baden-Württemberg’s Environment Minister Thekla Walker emphasized the regional impact: “Battery recycling holds great importance for Baden-Württemberg’s automotive sector. Closing the loop on the value chain reduces dependencies and increases resilience during supply chain disruptions.”
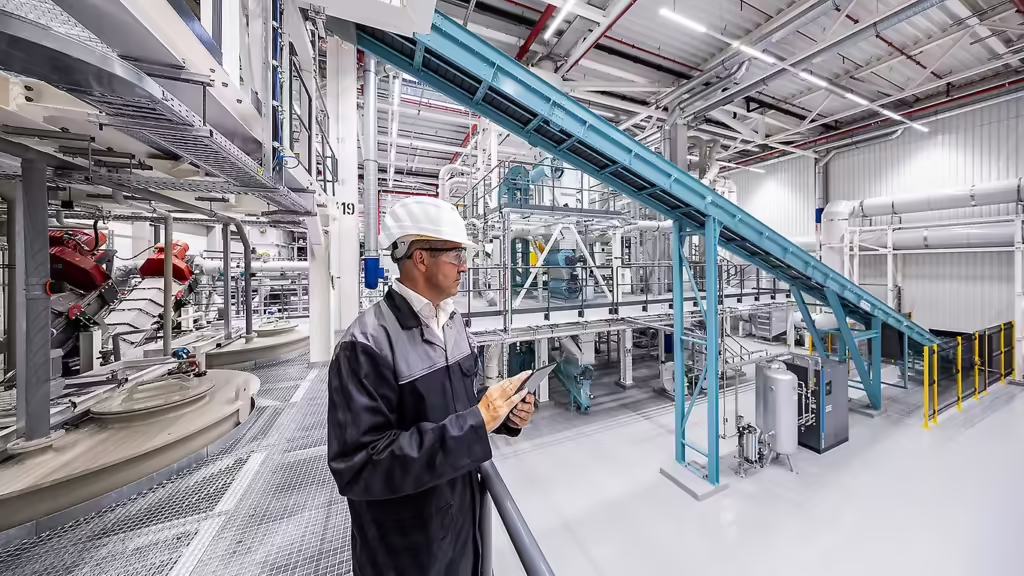
Mercedes-Benz’s circular approach extends beyond recycling. The company offers reconditioned batteries as spare parts and repurposes batteries for stationary energy storage through its subsidiary Mercedes-Benz Energy. The newly opened eCampus in Stuttgart-Untertürkheim focuses on developing new battery cell technologies with circularity in mind.
Industry analysts note that this development aligns with similar initiatives worldwide, including SK TES’s facility in Rotterdam and Ascend Elements’ operations in Poland. As global demand for electric vehicle batteries continues to rise, such recycling infrastructure becomes increasingly critical for sustainable manufacturing and raw material security.
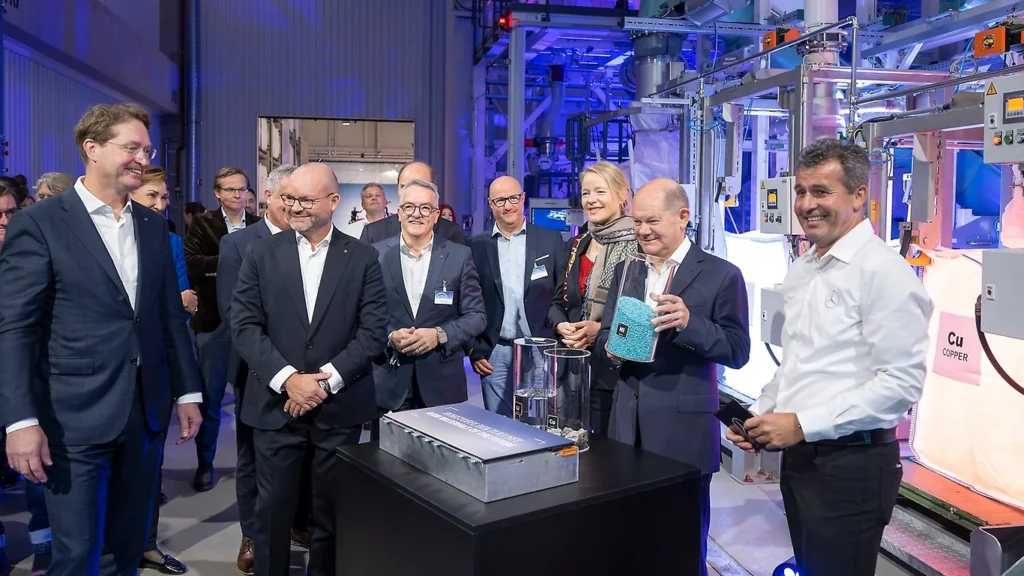
The facility’s process innovation and scale position it as a reference point for the automotive industry’s transition toward closed-loop manufacturing. With battery demand projected to increase substantially in coming years, the plant’s potential for scaled operations could influence similar projects globally.