In a technical advancement for automotive sustainability, Jaguar Land Rover (JLR) has successfully recycled polyurethane seat foam from end-of-life vehicles into new seat production. The initiative, developed at JLR’s Circularity Lab in Gaydon with partners Dow and Adient, creates a closed-loop supply chain for seat foam – a material traditionally destined for landfills.
The recycled foam will undergo production testing in early next year. Each new “circular seat” reduces CO2e emissions by 44 kg compared to conventional seats, equivalent to the energy needed to charge 3,000 smartphones.
Technical Process and Environmental Benefits
Initial laboratory testing has proven technical feasibility based on 20% closed-loop re-polyol content through Dow’s RENUVA sustainability program, with ongoing research aimed at increasing this percentage as high as viably possible.
“Close collaboration with experts from recycling and materials science industries, supply chain partners, and colleagues from design and engineering is key,” said Andrea Debbane, Chief Sustainability Officer at JLR. “We need to work as a collective value chain to unlock meaningful change at scale.”
Industry Collaboration and Implementation
Jon Penrice, Mobility President at Dow, explained: “Through chemical and advanced recycling processes, this breakthrough depolymerization closed-loop recycling solution meets requirements while maintaining superior comfort and quality of JLR seats.”
The initiative extends beyond seat foam. JLR’s Circularity Lab has achieved cost and environmental improvements in other components. Tests on front bumpers demonstrated identical quality with fewer polymers, projecting savings of 177,500 kg CO2e and £560,000 per model line.
More Stories
Broader Sustainability Context
This development aligns with JLR’s Reimagine strategy targeting carbon net zero across operations by 2039. The company joined the Ellen MacArthur Foundation Network in 2023, implementing circular economy principles across operations.
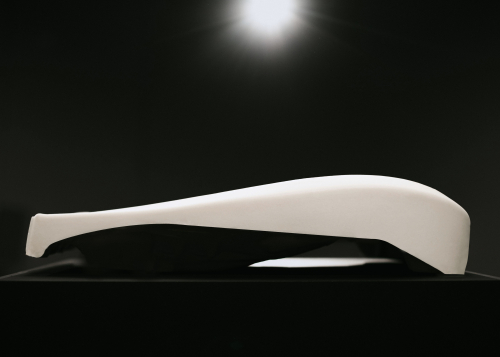
Mick Flanagan, Vice President Customer Group at Adient, noted: “By leveraging recycled polyurethane, we are setting new benchmarks for environmental responsibility while ensuring products deliver luxury and comfort customers expect.”
Historical Challenge and Future Impact
Traditionally, vehicle design overlooked end-of-life material separation. Mixed materials, fixing methods, and adhesives complicated recycling efforts. JLR’s cross-disciplinary approach now feeds data directly into vehicle development, ensuring recyclability while maintaining quality standards.
The company has achieved success in closed-loop innovation through an award-winning project that incorporated post-industrial waste from aluminum body panel stamping into new body panels. This involved creating a new aluminum grade suited to the closed-loop process through supply chain collaboration.