Fraunhofer IPA and acp systems AG’s new battery cell production system arrives at a crucial time for the energy storage industry. The newly commissioned winding system for cylindrical battery cells, housed at the Center for Digitalized Battery Cell Manufacturing (ZDB), offers flexibility in both formats and design – a first worldwide capability that could reshape battery manufacturing.
“At ZDB, we can cover all of the process steps involved in manufacturing a battery cell. The winding process is one of the core processes in cylindrical cell production, as the jelly roll is the centerpiece of the battery cell,” explains Julian Grimm, head of the research team at Fraunhofer IPA and Deputy Head of ZDB. “By bringing the winding system online, we have closed a gap in the fully digitalized process chain, so the production line is complete.”
The system’s core operation involves rolling positive and negative electrodes together with two separators to create what’s known in industry parlance as a “jelly roll.” This process demands precise positioning for assembly, where technicians insert a rod electrode through the roll’s central hole and weld it to the cylinder base.
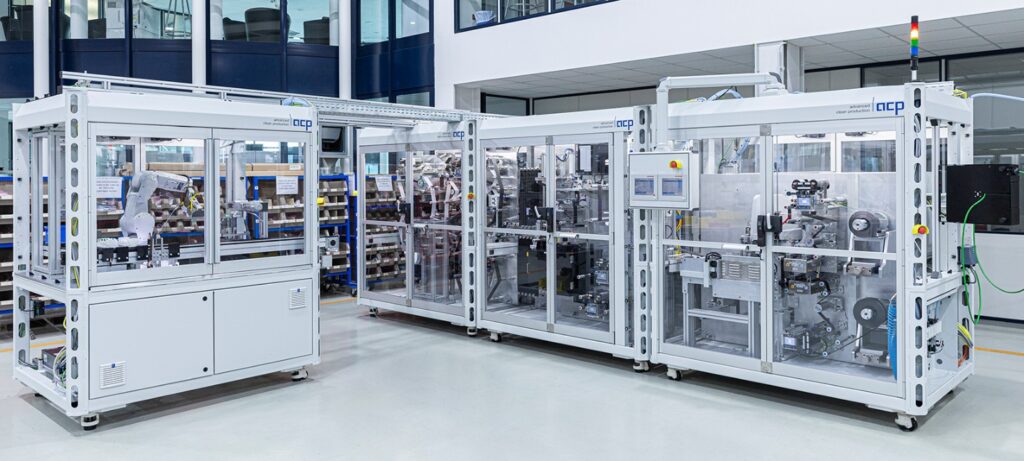
The Baden-Württemberg Ministry of Economic Affairs, Labour and Tourism backed the project financially, supporting a system that goes beyond traditional manufacturing limitations. The technology allows for various cell formats and tab designs, including tabless configurations – a technical advance that addresses current collection and heat dissipation challenges in larger format cells.
“What makes our system unique is its flexibility. It allows us to realize different cell formats in different sizes and tab designs, such as tabless designs, which don’t have a tab welded onto them,” Grimm notes. “The tab, a narrow terminal element on the anode and cathode that the electricity has to flow through, is the chokepoint in large-format cells.”
Similar Posts
The production line integrates digital monitoring throughout – from coating and winding to assembly, filling, and forming. Real-time cloud data collection via sensors could enable quality control and waste reduction. Fraunhofer IPA’s traceability technologies link collected data to individual cells, creating a comprehensive production record that aids in process refinement and error prevention.
As the automotive sector increasingly adopts cylindrical battery cells, with preferences moving toward larger formats, this system allows manufacturers to test new cell components and tab designs efficiently. The platform serves both research and production needs, particularly valuable for companies developing sodium-ion batteries and other emerging storage technologies.
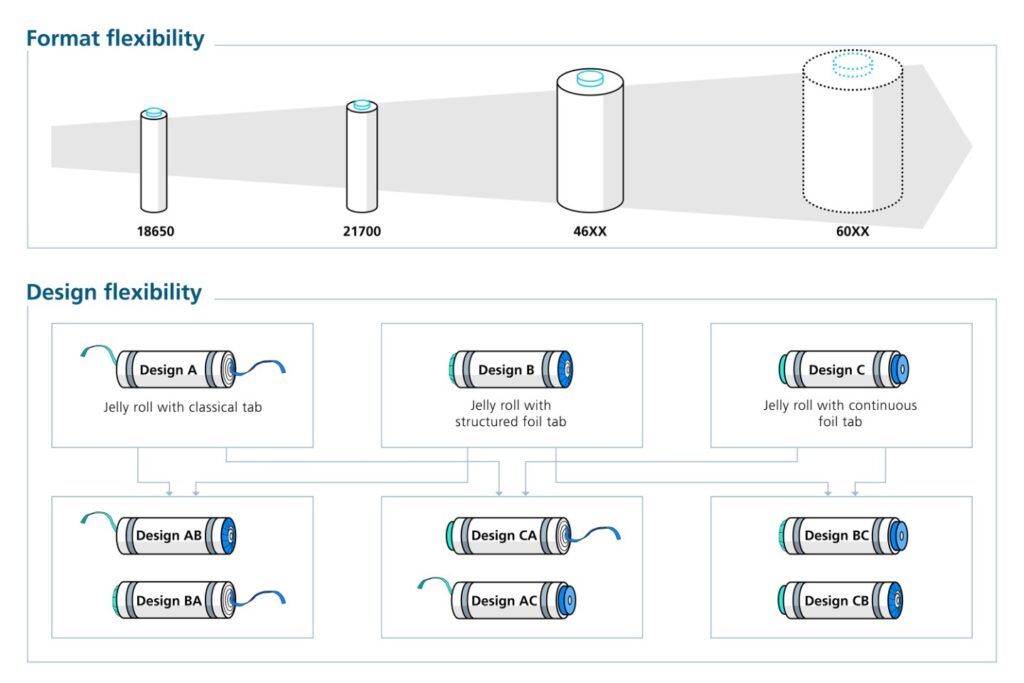
“Innovative cell designs require redesign and optimization of production processes, which we can study using the winding system,” Grimm adds. The facility welcomes manufacturers and users of electrodes, separators, and cells to test their prototypes, products, cell components, materials, and designs.
This development may place Europe firmly in the battery manufacturing landscape, offering the continent’s only complete production line for cylindrical cells in lithium-ion and future battery technologies. The system’s ability to produce larger cells with increased active material could lead to enhanced energy density – a critical factor for extending electric vehicle range.