Research teams from UWE Bristol and University of Southampton have engineered electronic textiles (e-textiles) that decompose naturally while maintaining medical-grade monitoring capabilities. The Smart, Wearable, and Eco-friendly Electronic Textiles (SWEET) project, published in Energy and Environmental Materials, addresses mounting concerns about electronic waste in textiles – a sector generating 92 million tons of waste annually according to a report by Global Fashion Agenda.
The e-textiles feature precision-engineered trilayer architecture: a Tencel lyocell base fabric manufactured from dissolved wood pulp cellulose, a sensing layer incorporating graphene-enhanced conductive polymers, and an interface layer joining these components. The active electronics use graphene combined with poly(3,4-ethylenedioxythiophene):polystyrene sulfonate (PEDOT:PSS) – a conductive polymer composite where PEDOT provides electrical conductivity while PSS enhances water solubility.
“Integrating electrical components into conventional textiles complicates recycling because it often contains metals, such as silver, that don’t easily biodegrade,” explains Professor Nazmul Karim from Southampton’s Winchester School of Art. “Our potential ecofriendly approach for selecting sustainable materials and manufacturing overcomes this, enabling the fabric to decompose when it is disposed of.”
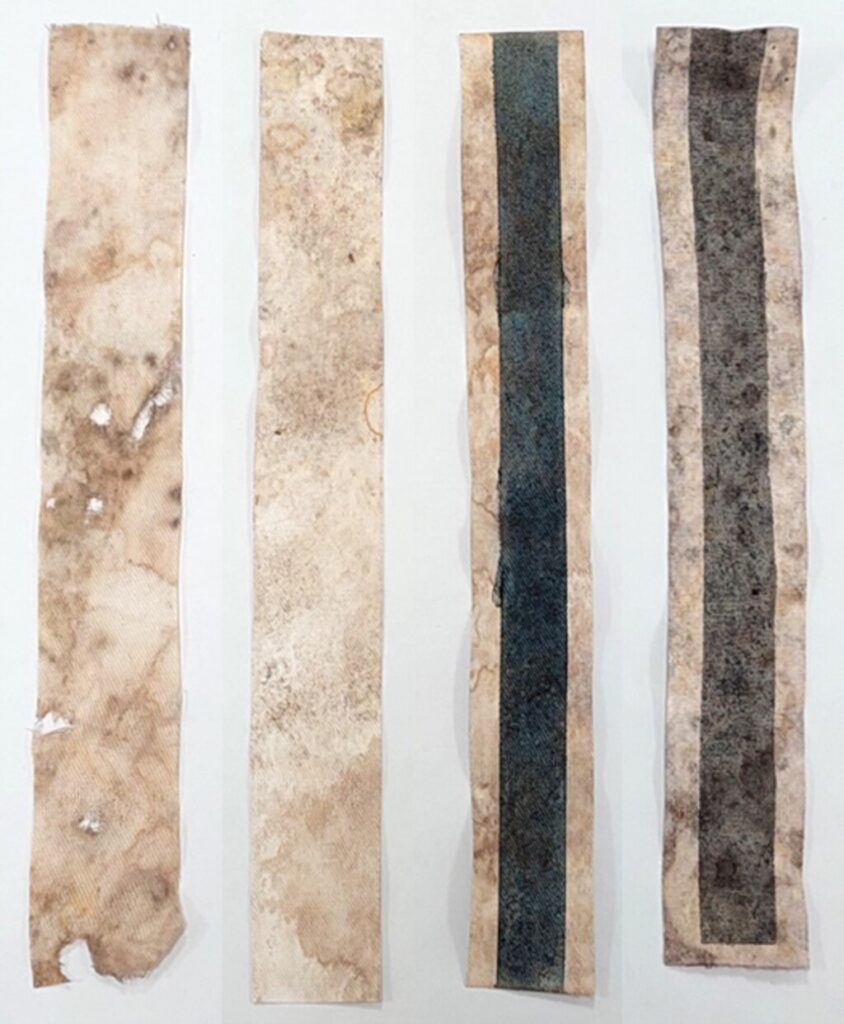
Laboratory testing demonstrated the material’s medical monitoring capabilities. Five volunteers wore gloves with attached SWEET fabric swatches connected to physiological monitoring equipment. The e-textiles accurately measured heart rate and temperature at medical device industry standards – critical for potential healthcare applications targeting 640 million people worldwide affected by heart conditions.
Environmental performance metrics proved compelling: soil burial tests showed 48% weight loss and 98% strength reduction within four months. Life cycle assessment revealed graphene-based electrodes reduced environmental impact 40-fold compared to conventional metal electrodes. The precision inkjet printing manufacturing process eliminated material waste while cutting water and energy usage versus traditional screen printing methods.
“Our life cycle analysis shows that graphene-based e-textiles have a fraction of the environmental footprint compared to traditional electronics,” notes lead author Marzia Dulal, Commonwealth PhD Scholar at UWE Bristol. This aligns with urgent sustainability needs – electronic waste reached 53.6 million metric tons globally in 2019, with only 17.4% recycled according to the UN Global E-waste Monitor.
Similar Posts
The research builds on previous work in biodegradable electronics, including University of Stanford’s 2021 development of recyclable semiconductors and MIT’s compostable sensors using cellulose. However, SWEET’s innovation lies in achieving medical-grade monitoring while ensuring complete biodegradability.
Dr. Shaila Afroj, Associate Professor at Exeter University, emphasizes practical implications: “Achieving reliable, industry-standard monitoring with eco-friendly materials demonstrates sustainability doesn’t compromise functionality, especially in critical applications like healthcare.”
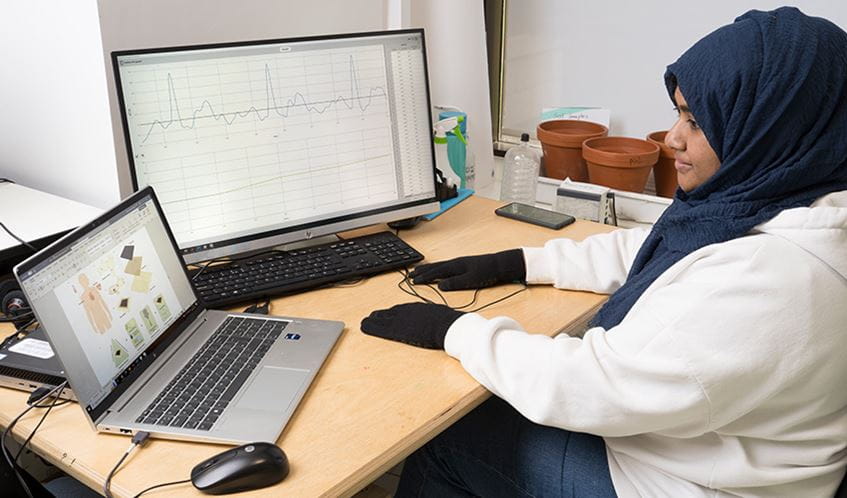
The e-textiles market, valued at $4.3 billion in 2022, faces growing pressure to address sustainability. Current e-textiles often rely on silver nanoparticle coatings and metallic fibers that persist in landfills. While SWEET technology offers a biodegradable alternative, challenges remain around scaling production, ensuring consistent performance across manufacturing batches, and maintaining electronic functionality throughout the product lifecycle.
Research continues into wearable applications for early detection of cardiovascular conditions. However, regulatory approval, durability testing, and cost-effective mass production require further development before commercial implementation.
The polymer science and sustainable materials communities monitor these advances closely. As global textile waste mounts and electronics become increasingly integrated into daily wear, biodegradable alternatives may help mitigate environmental impact while advancing wearable healthcare technology.